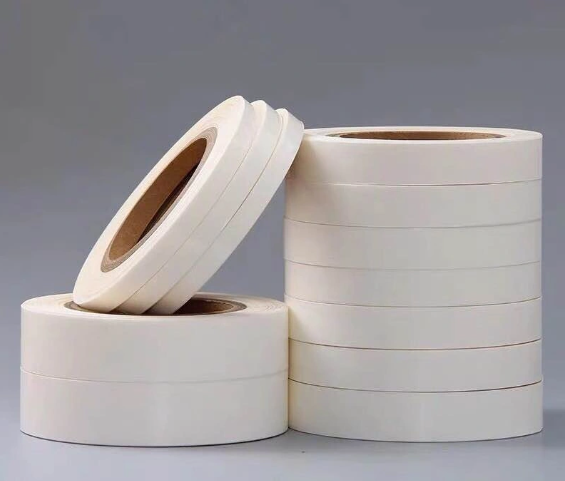
일반적인 핫 멜트 접착제 필름 형성 방법은 무엇입니까?
코팅 방법 코팅 방법은 일반적으로 릴리스 필름을 생성하는 데 사용됩니다. 코팅 방법은 스무드 롤 코팅, 텍스처 코팅, 블레이드 코팅, 스프레이 코팅 및 커튼 코팅으로 나눌 수 있습니다. 다른 제품에 따르면, 다른 코팅 특성이 채택되고 다른 코팅 방법이 사용됩니다. 코팅 방법에 의해 생성 된 방출 필름의 주요 특성에는 코팅 균일 성, 높은 잔류 접착력, 평탄도 및 높은 청결성이 포함됩니다. 블로우 몰딩 수지는 압출기에 의해 녹고 가소화되고 환형 머리로부터 수직 위로 위로 끌어 당겼다. 팽창 된 후, 헤링본 플레이트에서 트랙션 롤러에 도입 한 다음 완제품은 가이드 롤러 및 코일 링 장치를 통해 얻습니다. 블로우 성형 방법은 인플레이션 공정으로 인해 생성물의 수직 및 수평 분자가 다른 정도로 늘어납니다. 제품의 온도 저항 및 열 밀봉 성능은 크게 영향을받습니다. 캐스팅 방법 수지는 압출기에 의해 녹고 가소화되고 슬릿 다이를 통해 다이 헤드에서 압출되어 용융 물질이 냉각 롤러에 가까워지고 완성 된 제품은 껍질을 벗기, 스트레칭, 슬릿팅 및 롤링으로 얻습니다. 주조 방법의 생산 효율은 매우 높으며 제품 품질은 안정적입니다. 생산 공정에는 낭비가 적고 가장자리와 폐기물의 온라인 재활용을 실현하는 것이 더 쉽고 재료의 활용률이 높습니다. 블로우 성형 대 캐스팅 Blow Molding 방법에 사용 된 환형 다이 및 다층 다이 코어는 가공 정확도 및 어셈블리 정확도에 대한 요구 사항이 매우 높으며 제어하기가 특히 어렵습니다. 가공 및 일치 정확도에 작은 오류가있는 경우 조정으로 보상 할 수 없으므로 제품의 두께는 공차가 기본적으로 약 ± 10%입니다. 주조 방법은 평평한 다이 헤드를 채택하고 다이 헤드에 특별한 보유 홈이있어 재료 흐름의 균일 성을 보장 할 수 있으며, 다이 립 갭의 균일 성은 자동 조정 장치에 의해 자동으로 제어 될 수 있습니다. 다이 헤드, 제어 정확도는 매우 높습니다. 두꺼운 필름은 ± 3% 이하로 제어 할 수 있습니다. Blow Molding은 약간의 핫 멜트 접착제 필름 제품을 생성 할 수 있지만, 필름의 평탄성과 균일 성은 캐스팅 필름의 것만 큼 좋지는 않습니다. 큰 수축은 쉽게 할 수 있습니다 결합이 좋지 않습니다 캐스팅 방법에 의한 필름 제작 필름의 분자 배열은 순서대로, 제품의 냉각 속도는 빠르며, 이는 제품의 투명성, 광택 및 두께 균일 성을 향상시키는 데 유리하며 제품 텍스처는 부드럽고 힘든 일입니다. ; 충격 저항, 내열성 및 저온 적응성은 블로우 성형보다 낫습니다. 캘린더링 수지는 압출기에 의해 녹고 발성하여 슬릿 다이를 통해 다이 헤드에서 압출 된 후 3 롤 캘린더에 의해 롤링되고 냉각 된 다음 냉각 운송 롤러와 코일 링 장치를 통과하여 완제품을 얻습니다. 캘린더 방법은 다양한 제품 성능 표시기, 두께 균일 성 및 제품 열 수축에서 블로우 성형 방법보다 우수합니다. 캘린더링은 또한 제품 두께 범위와 원료 적응성에서 큰 이점을 가지고 있습니다. 그러나 투자 측면에서 캘린더링 프로세스는 블로우 성형 공정보다 10 배 이상 높습니다. 주조 방법과 비교할 때 동일한 규모의 생산 라인은 수직 작동을 채택하기 때문에 작동이 더 복잡하고 어렵고 주조 방법은 두께가 1.5mm 이상인 제품을 생산할 수 없습니다.